Working principle and advantages of vacuum casting
Release time:
2025-05-08 16:24
Vacuum casting is a versatile manufacturing process widely used for producing high-quality prototypes and small production runs of various parts. This method involves creating a silicone mold from a master model, which is then placed in a vacuum chamber. Once the chamber is evacuated, the liquid casting material—typically polyurethane resin—is poured into the mold. The vacuum ensures that air bubbles are removed, resulting in a smooth and precise finish on the final product. One of the significant advantages of vacuum casting is its ability to replicate intricate details and complex geometries, making it an ideal choice for industries such as automotive, aerospace, and consumer goods. Additionally, vacuum casting allows for the use of various materials, enabling designers to select options that closely match the desired properties of the final product, such as flexibility, hardness, or temperature resistance. This process not only reduces lead times compared to traditional manufacturing methods but also minimizes waste, making it a more environmentally friendly option. As technology continues to evolve, vacuum casting is becoming increasingly accessible and efficient, further solidifying its role in the rapid prototyping landscape and enhancing innovation across multiple sectors. Key Benefits cooperating with GD prototyping are quality, speed, versality and low cost effectiveness. In general, we can realize prototypes or low volume production via this process before making injection molding products.
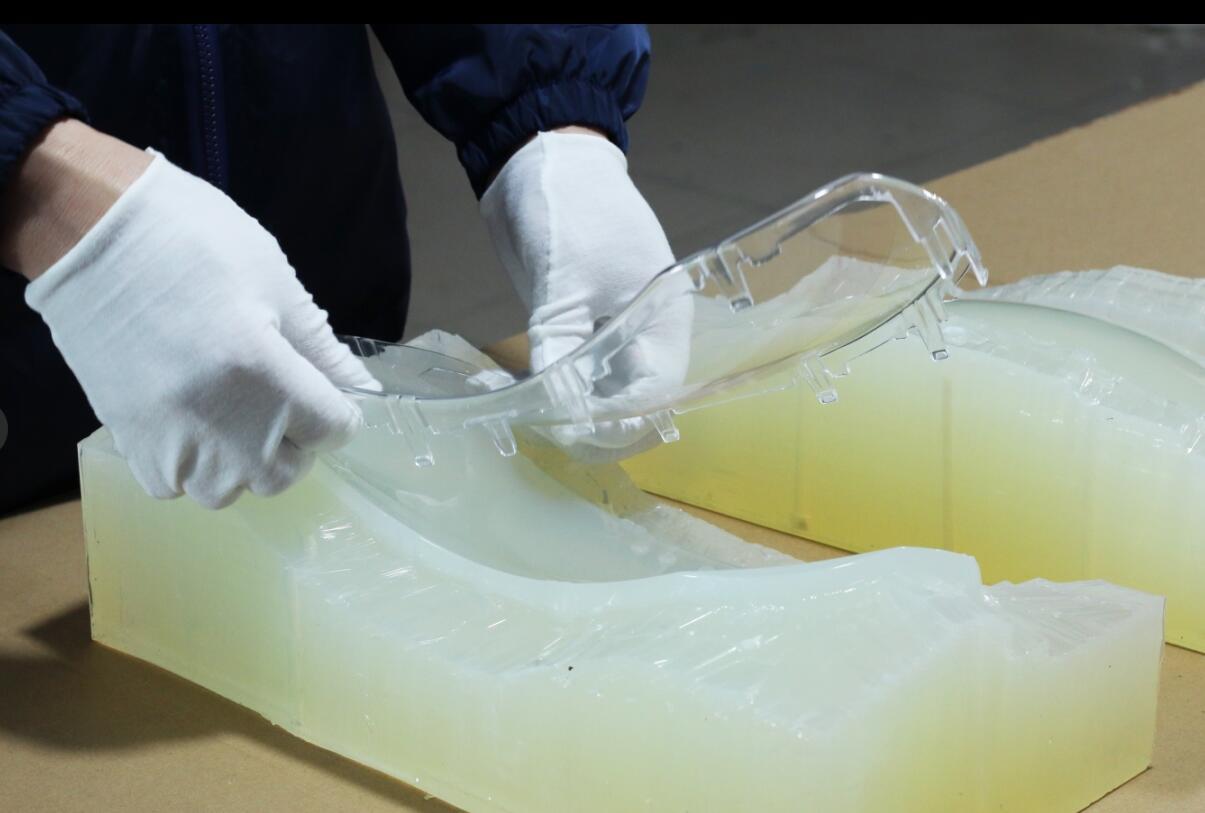
Working principle of vacuum molding
Vacuum molding technology mainly relies on molds, vacuum systems and molding materials. Its working principle can be summarized as follows:
1. Prepare a prototype or model: First, you need to prepare a prototype or model, which can be a solid model made by other process means.
2. Prepare the mold: According to the prototype or model, make a reverse mold. This mold will be used to replicate the shape and size of the prototype or model.
3. Vacuum system: Install the mold in a vacuum system to ensure good sealing between the mold and the vacuum system.
4. Material processing: Pour liquid or semi-solid molding materials into the mold. These materials can be plastics, metals, ceramics, etc.
5. Vacuum molding: In a vacuum environment, the material is evenly distributed and solidified in the mold. This process allows the replica to obtain the same shape and size as the prototype or model.
6. Cooling and demolding: After the material solidifies, it is cooled and demolded to obtain a high-precision replica.
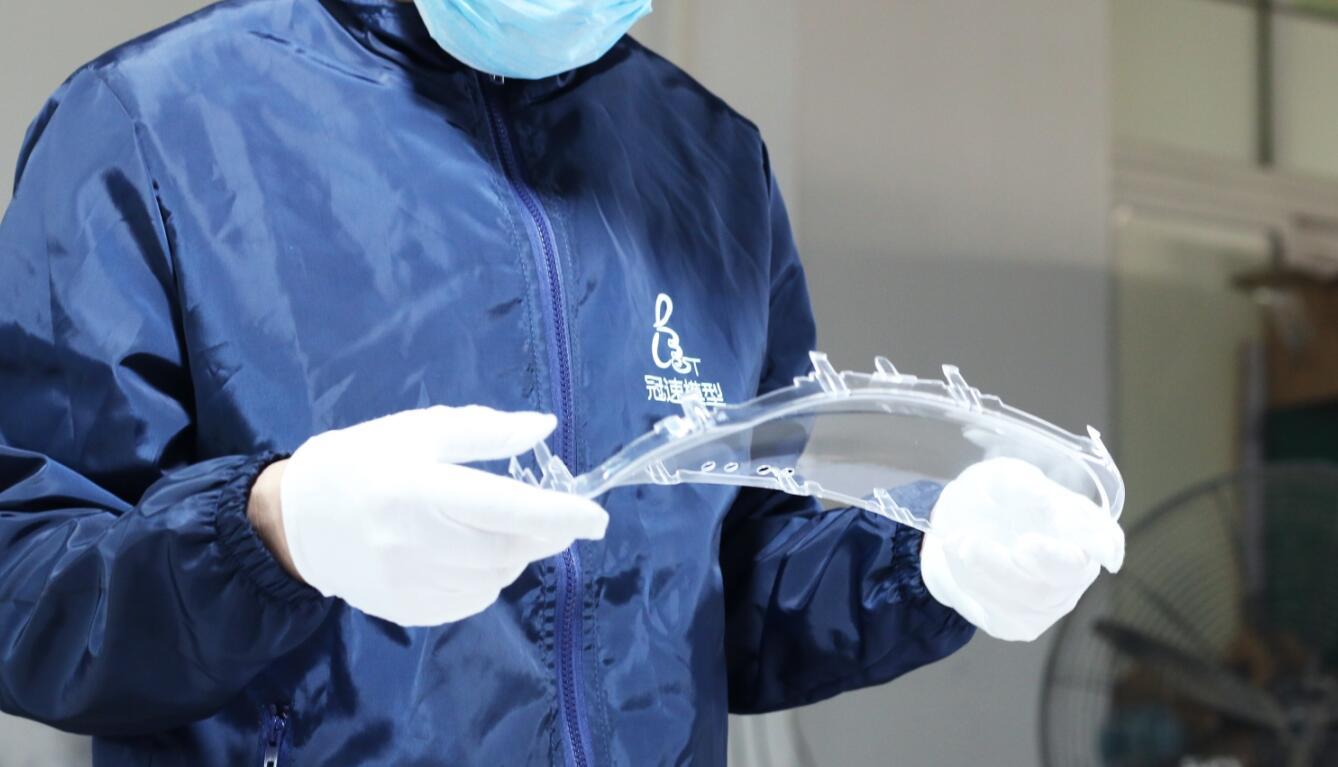
Advantages of Vacuum Casting
1. High-precision replication: Vacuum casting technology can achieve high-precision replication, ensuring that the replica is highly consistent with the prototype or model in shape, size and surface quality.
2. Efficient production: Compared with traditional manufacturing methods, vacuum casting has a shorter manufacturing cycle and higher production efficiency.
3. Reduce costs: Due to the short manufacturing cycle and high material utilization rate, vacuum casting can reduce manufacturing costs, especially when a large number of replicas are required.
4. Wide application: Vacuum casting technology is suitable for a variety of materials, including plastics, metals, ceramics, etc., making it widely used in many fields.
5. Suitable for complex shapes: For parts with complex shapes and structures, vacuum casting technology can easily replicate their details and features.
6. Improve product quality: Replicas made by vacuum casting technology have consistent size and performance, which helps to improve product quality.
7. Environmental protection and energy saving: Since vacuum casting technology has a high material utilization rate and low energy consumption, it is an environmentally friendly manufacturing method.
8. Customized production: Vacuum molding technology can be customized according to customer needs to meet the needs of different customers.
9. Easy to operate and maintain: The operation of vacuum molding equipment is relatively simple and easy to maintain, which can reduce labor costs and maintenance costs.
10. Wide range of applications: Vacuum molding technology is not only suitable for large-scale production, but also for small-batch production, making it widely used in various production scales.
In short, vacuum molding technology is an advanced manufacturing process with advantages such as high-precision replication, efficient production, cost reduction, and wide application. It has broad application prospects in manufacturing, automobiles, aerospace, electronics and other fields. With the continuous advancement of technology and the reduction of costs, vacuum molding technology will be applied and promoted in more fields.
Vacuum casting
preceding page
preceding page
Related News
2024-04-05