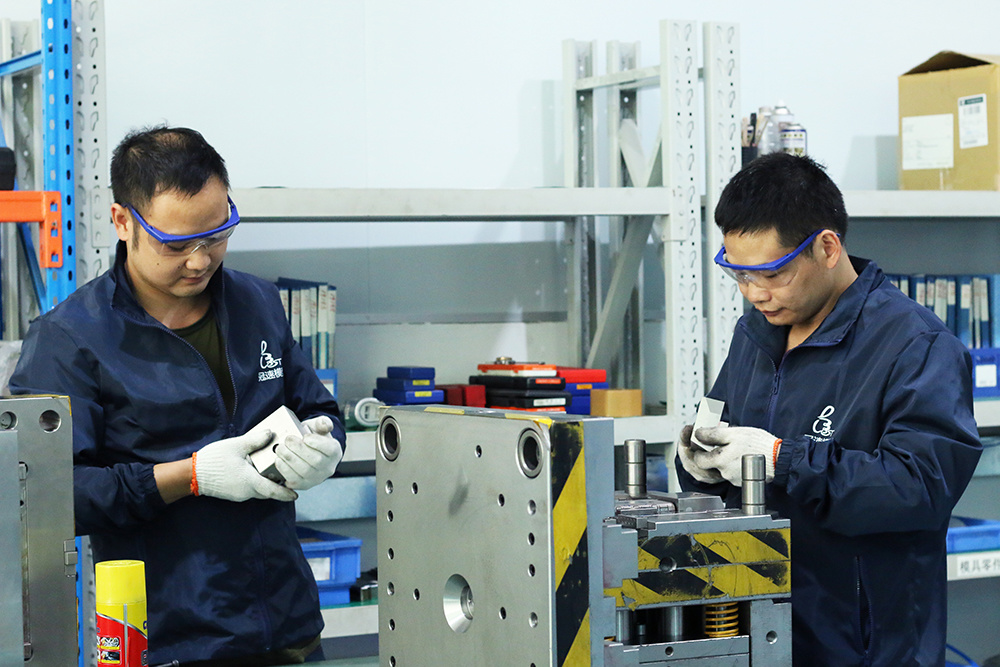
Production Capabilities
Our project management team consists of skilled production and engineering personnel who are dedicated to meeting specific delivery needs. This level of dedication means that machining start times are adhered to and that integrated systems and lean-manufacturing-based project management tools are utilized to track the progress of each order.
Injection molding is a manufacturing process for producing plastic parts by injecting molten material into a mould,which is most typically used in mass-production processes where the plastic part is being created thousands or even millions of times in succession.
Die casting is a metal casting process that is characterized by forcing molten metal under high pressure into a mould cavity. The mould cavity is created using two hardened tool steel dies which have been machined into shape, also for producing large quantity.
Precision casting is a process in which the metal is melted into a liquid meeting certain requirements and poured into the casting mold. After cooling, solidification and cleaning, the casting with predetermined shape, size and performance can be obtained.
What is Injection Molding
At GD prototyping we specialize in producing high-quality plastic injection molded parts and mold tools. We offer machining and finishing services to make tools from a variety of materials, and can produce 50 to 100,000+ finished parts in a wide variety of plastics. With advanced material verification and quality processes we can ensure your tools and parts exceed your expectations.
Advantages of Injection Molding
◆ A wide variety of plastic materials
◆ Large volume in short timeline
◆ Stable and reliable process
◆ Long term mold and for production
◆ Premium quality
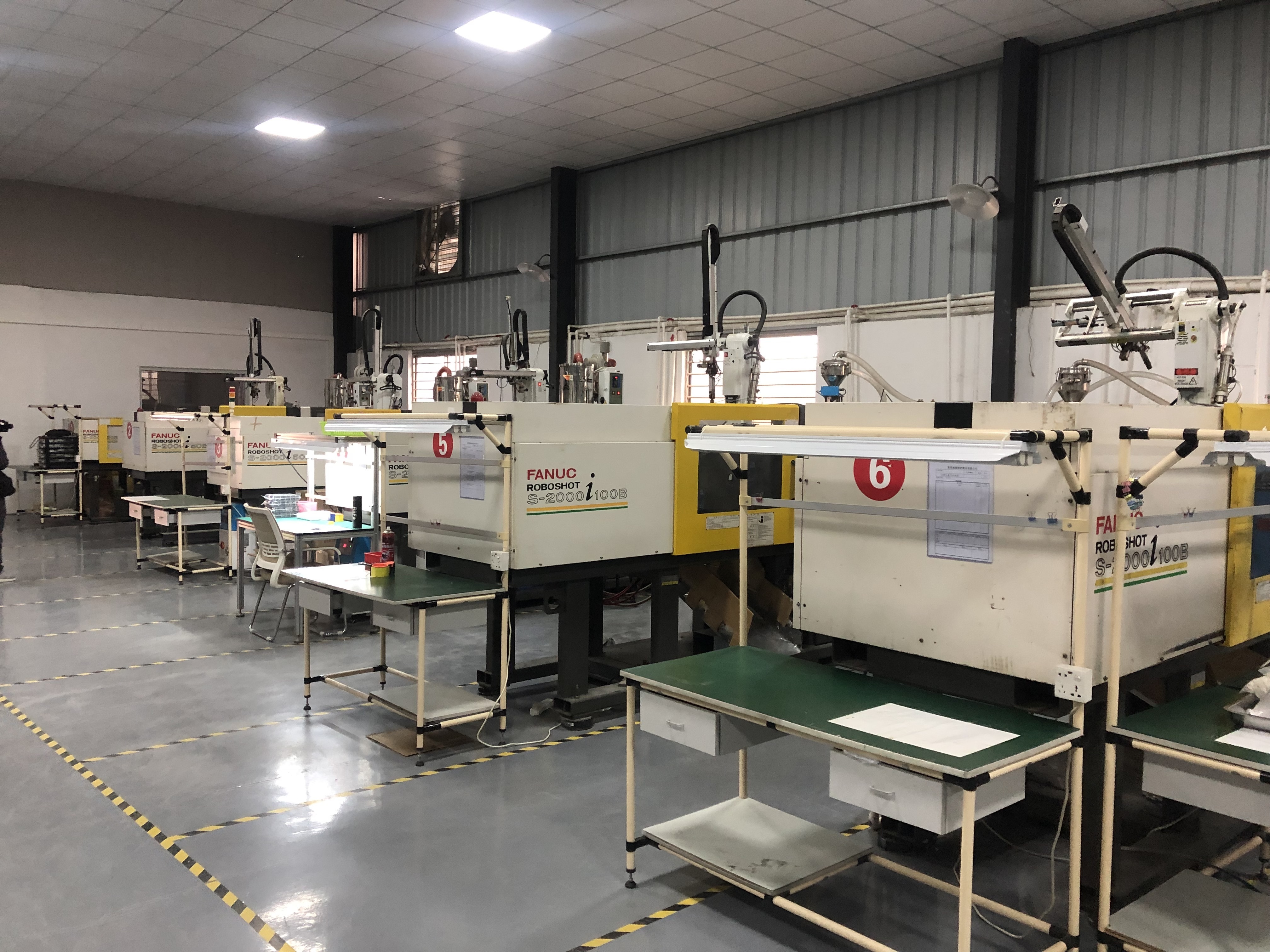
Injection Molding Capabilities
01
Rapid tooling
Most choice for the low volume production, using the aluminum inserts with a life time of up to 20,000 run, typically 1-2 weeks, it can reduce leadtime .
02
Production tooling
A stable and reliable mold process for mass production,machined in typically 3-4 weeks, with a life time up to 100,000.
03
Multi-cavity molds
Multiple identical cavities are machined into the mold tool. This allows for more parts to be produced simultaneously per shot, not only leveraging the manufacturing efficiency but also minimizing the unit costs.
04
Overmolding
Adding an additional layer of material over an already existing molded piece or part.

What is Vacuum Casting
Name | Description |
Minimum order quantity | 200 runs |
Mold material | Tool Steel P20, Carbon Steel S50C, Aluminum |
Mold types | Rapid tooling, production tooling |
Mold storage | Minimum 2 years and we will do the maintenance for the mold. |
Mold lead time | 2-3 weeks (Rapid tool), 4-5 weeks (Production tool) |
Quality assurance | DFM Analysis, Moldflow, CAE, Control Plan, PSW Inspection reports included, full dimensional report and material certifications available upon request, PPAP submitted after starting the production. |
Sample verification program | Similar to First Article Inspection, you will receive 2 sets of parts upon the machining of the mold to test fit before continuing with full production. |
Mold remachining | We can remachine the molds should any changes be required, changes to be reviewed on a case by case basis. |
Reorders | Unit price is based on the quantity required for the reorder with an additional set up fee of $150/€120. |
Die Casting
Die casting is generally the lowest cost method for producing complex-shaped components from aluminium alloys, and so rheocasting should also have the potential for low cost production. Die-casting is an economical way of producing large quantities of complicated shaped products of light metals with high precision. Melted metals are introduced at a high speed into the water-cooled metal die or mold through an injection process. The molten metal turns into a solid when in contact with the cool water. When the solidification and mold casting process has completed, the mold is opened and the ejection of parts initiated via a mechanical activation of the ejector pins. The die is subsequently exposed to air, sprayed with a lubricant, closed, and molten metal injected once again into the die to complete the cycle.
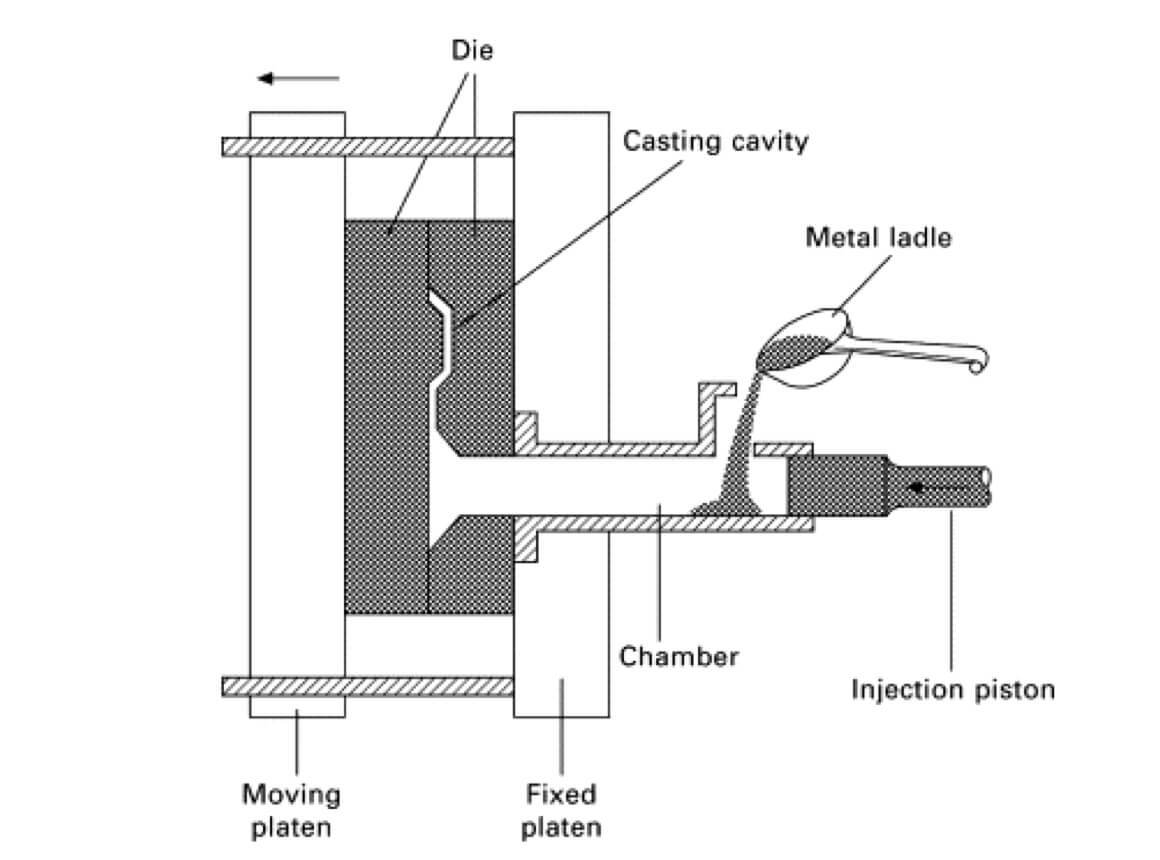
Advantages of Die Casting
Flexibility for the production of metal components.
Particularly suited for comparatively complex near-net shape parts.
High production rates and good dimensional repeatability.
Long term and even permanent mold used
Economical Cost for large quantities production
Die Casting Capabilities
Rapid Tooling
Most choice for the low volume production, using the aluminum inserts with a life time of up to 20,000 run, typically 1-2 weeks, it can reduce leadtime .
Low-Pressure Die Casting
in which the metal is forced into the mold with air pressure for mass production,machined in typically 3-4 weeks, with a life time up to 100,000
High-Pressure Die Casting
In which a hydraulic ram is used to inject the molten metal into the die at extremely high pressures not only leveraging the manufacturing efficiency but also minimizing the unit costs.
Gravity Permanent Mold Casting
This process use the metal die in combination with a gravity-fed metal delivery system. This combination lowers the overall cost of the process while taking advantage of the higher cooling rate of the metal die. The advantages and limitations of this system are similar to those of the LP permanent mold systems.
Name | Description |
Minimumorder quantity | 100runs |
Moldmaterial | ToolSteelP20,CarbonSteelS50C,Aluminum |
Moldtypes | Rapidtooling,productiontooling |
Moldstorage | Minimum2yearsandwewilldothemaintenanceforthemold. |
Moldleadtime | 2-3weeks(Rapidtool),4-5weeks(Productiontool) |
Qualityassurance | DFMAnalysis,Moldflow,CAE,ControlPlan,PSWInspectionreportsincluded,fulldimensionalreportandmaterial certificationsavailableuponrequest,PPAPsubmittedafterstartingtheproduction. |
Sampleverificationprogram | SimilartoFirstArticleInspection,youwillreceive2setsofpartsuponthemachiningofthemoldtotestfitbefore continuingwithfullproduction. |
Moldremachining | Wecanremachinethemoldsshouldanychangesberequired,changestobereviewedonacasebycasebasis. |
Reorders | Unitpriceisbasedonthequantityrequiredforthereorderwithanadditionalsetupfeeof$150/€120. |
Die Casting Capabilities
Lost-wax process, also called cire-perdue, method of metal casting in which a molten metal is poured into a mold that has been created by means of a wax model. Once the mold is made, the wax model is melted and drained away. A hollow core can be effected by the introduction of a heat-proof core that prevents the molten metal from totally filling the mold. Common on every continent except Australia, the lost-wax method dates from the 3rd millennium BC and has sustained few changes since then.
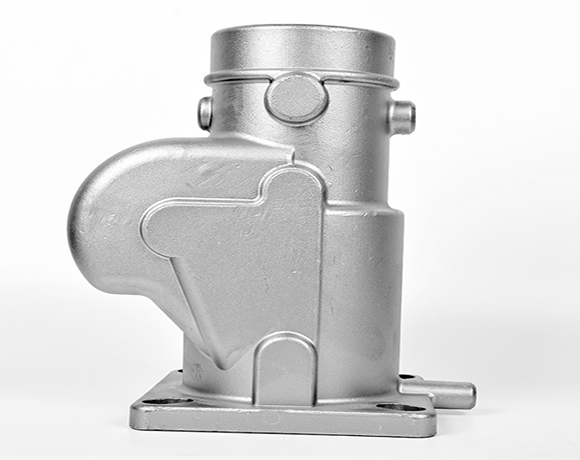
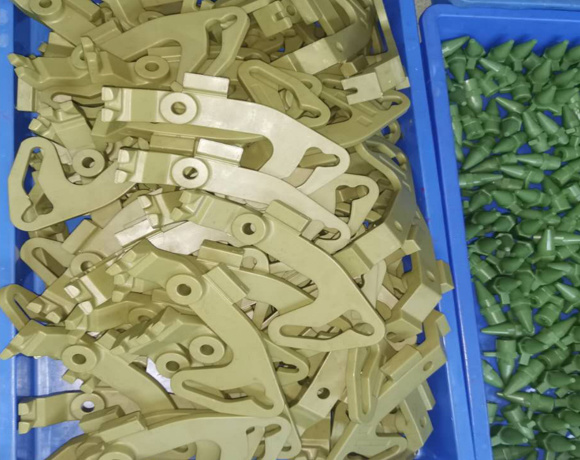
Sand casting, the most widely used casting process, utilizes expendable sand molds to form complex metal parts that can be made of nearly any alloy. Because the sand mold must be destroyed in order to remove the part, called the casting, sand casting typically has a low production rate. The sand casting process involves the use of a furnace, metal, pattern, and sand mold. The metal is melted in the furnace and then ladled and poured into the cavity of the sand mold, which is formed by the pattern. The sand mold separates along a parting line and the solidified casting can be removed. The steps in this process are described in greater detail in the next section.
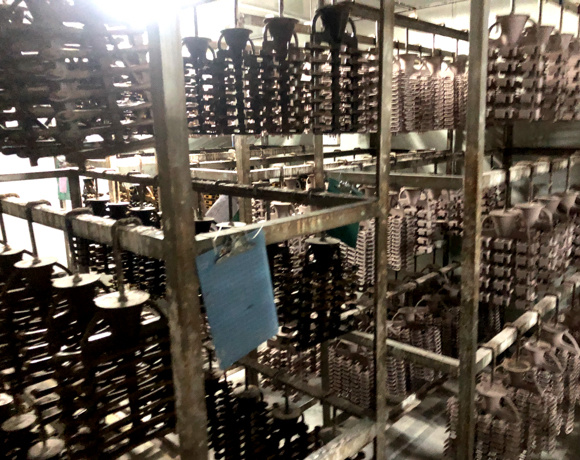
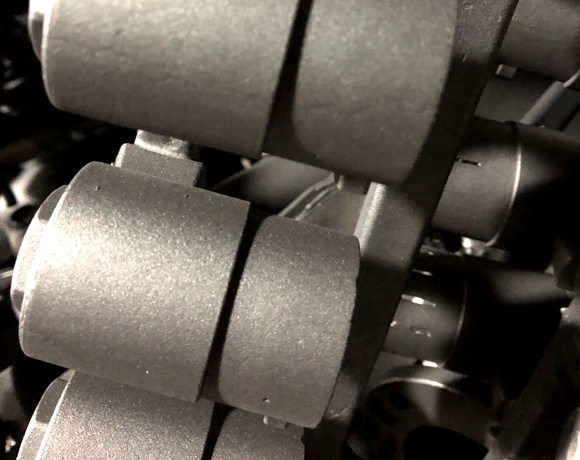
What is Vacuum Casting
With our investment casting process, you have a wide selection of nickel, cobalt, duplex, super alloy, stainless, heat and wear resistant and alloy steels that will produce the most complex, finely detailed lost wax castings possible. Working with us you can make informed decisions based upon the design specifications and the ultimate use of the product. Our goal is to see you be successful and have you as a repeat customer for years to come. Together, we can explore your opportunities. You, our highly valued customer, will always have executive decision-making powers and the last word when it comes to helping us create the precision casting that will serve you best.
What is Vacuum Casting
Why Choose Production Projects With GD prototyping
Competitives Prices:For production projects we will strive to provide customer with the most favorable prices,we lead the industry with fair pricing,especially compared with other suppliers in USA , EU or Other Asian Region, the most accurate prices will be given after evaluating by our engineers.
Quality Assurance:Best Prototypes performs first article and in-process inspections for all machining and molding operations. Inspection data and Certificates of Conformance are provided to customer specifications. We place great emphasis on traceability by documentation: Full dimensional inspection reports, customer-approved control plans, material certifications, Design Failure Modes and Effects Analysis (DFMEA),Process Failure Modes and Effects Analysis (PFMEA), Initial Process Studies, Part Submission Warrant (PSW)and PPAP Level 1,2,3,4,5.
Project Management:Our Project Managers (PMs) are assigned directly to the customer to ensure we have a "single point of contact" communication process. This single point of contact process enables our PMs to represent the voice of the customer, to communicate accurate and timely information, and to streamline the design and tool build process. As the direct focal point to the customer, our PMs manage the customer's project from concept inception to final delivery of that product.
Technical Support:Starting from customer's RFQ, DfM analysis and Mold Flow will be sent upon quoting, and as well as with design and material feedbacks, and during the production, our skilled mechanical engineer will provide technical support on your project.Our engineers are integrated into both the assembly and machining centers providing value-add engineering support. Engineering's core competencies include:Industrial design assistance,3D cad design & modeling,Custom design, feasibility analysis and bill of materials (BoM),Defining fabrication / assembly / configuration, test, and quality systems

Preliminary Review
· Detailed review and documentation of the product requirements
· Identify requirements, conflicts, and risks
· Review BOM and cost estimate to ensure no pricing changes and item availability for purchased components

First Article Build
·Record, document, and update assembly procedures
· Evaluate and perform design verification
· Bulid prototypes to do the preliminary testing- definition and execution of testing procedures
· Update all documentation in preparation for production build

Production Build
·Review BOM and develop a procurement plan identifying any cost savings for higher- volume purchasing/long lead time items · Finalize testing procedures and requirements
· Create detailed production schedule for years 1-3
Picture Display
We offer a wide range of CNC machining services including milling and turning of various materials, as well as drilling, tapping, EDM (Electrical Discharge Machining), and wire EDM.
Online Message
If you are interested in cooperation, please contact us immediately and we will give you feedback as soon as possible!